Principal Investigator
:
Prof. dr hab. inż. Ryszard Pałka
West Pomeranian University of Technology in Szczecin
Panel: ST8
Funding scheme
: OPUS 9
announced on
16th March 2015
Attempts to use electric motors to power automotive vehicles have been made for many years and intensified especially in the times of successive fuel crises (for instance, General Motors presented a technologically advanced EV1 model as far back as the mid-1990s). European car manufacturers, however, failed to rise to the challenge of designing and implementing the production of electric cars at the time.
Electric Controlled Permanent Magnet Excited Synchronous Machine: a) model, b) magnetic field distribution
Nearly all automotive companies have by now added electric cars to their portfolio. More and more models are being developed, but vehicles of this type still continue to be treated as a technological novelty. This is a misconception, since electric drives have competed with diesel engines since the dawn of the automotive industry. As far back as the end of the 19th century, customers were able to purchase horseless vehicles equipped with electric motors, and the 100km/h speed barrier was first broken in 1899 by an electric vehicle: the Belgian La Jamais Contente.
The chief obstacle to mastering electric car technology has to do with the source of electricity, which puts very rigorous demands on other components of the system (primarily the engine). For this reason, electric engine design must take account of the associated limitations. The power unit must also be optimally adjusted to the standard driving cycle. This means that the weight and size of the engine should be reduced to the minimum, without compromising the processing of energy across the entire range of rotational speeds.
Electric Controlled Permanent Magnet Excited Synchronous Machine
Electric motors currently in use in hybrid and electric cars have many important drawbacks; their dimensions, and also power systems, must be considerably resized to guarantee adequate torque at the outset (at small rotational speeds). The parameters of the currently preferred solutions using permanent magnets are also unsatisfactory, especially at high rotational speeds. In order to neutralize these effects, various techniques for reducing magnetic flux in the machine have been introduced. The conventional approach to the problem involves regulating the excitation current so as to generate a magnetic field opposite to the field of the magnets and thus reduce the latter. This complicates the system and makes it larger.
Electric Controlled Permanent Magnet Excited Synchronous Machine
In order to address these issues, our research project, conducted within the framework of the OPUS 9 funding scheme, has developed a completely new high-speed permanent magnet machine, which allows magnetic flux to be regulated (the Electric Controlled Permanent Magnet Excited Synchronous Machine, ECPMSM). It is a combination of a disc-type machine with a transverse flux machine, characterised by the presence of an additional magnetic excitation system, and also high efficiency across the entire spectrum of rotational speeds and loads. The machine boasts a large starting torque and its rotations are easy to regulate. These properties meet all the current requirements of the automotive industry, such as high environmental standards, economic efficiency and small size. Mastering the production technology for an electric engine of this kind would reduce the technological gap that separates our country from developed European ones in this major sector of the economy.
Our research under OPUS 9 involved building and testing several prototypes of innovative permanent-magnet machines with flux regulation. Our results have been published in several dozen articles and presented at more than ten conferences. We also took out 4 national patents on our hybrid machine solutions.
Project title: Use of hybrid excited synchronous machines in construction of highly efficient car drives
Prof. dr hab. inż. Ryszard Pałka
Ryszard Pałka graduated summa cum laude from the Faculty of Electrical Engineering at the Szczecin University of Technology (1976) and defended his doctoral thesis at the Faculty of Electrical Engineering at the Poznań University of Technology (1979), before being awarded the title of habilitated doctor at the Institute of Electrical Engineering in Warsaw (1986). In 1983-84, he held a fellowship from the Alexander von Humboldt Foundation at the Institute of Electrical Machines, Traction and Drives of the Technical University of Braunschweig (Germany), where he continued to work between 1988 and 2005. He is currently employed at the Faculty of Electrical Engineering at the West Pomeranian University of Technology in Szczecin. He is the author of more than 300 articles published in Polish and international journals, as well as 6 national patents. He has participated in several research grants awarded by the National Science Centre and the National Centre for Research and Development, and nearly 25 commissions for companies such as Siemens, Bosch, Volkswagen, BMW, Atlas-Copco, Linde, Thyssen, Nexans, Philips, AEG, RWE and Daimler-Chrysler. He actively collaborates with research centres in Germany, Italy, England, Canada, South Korea and China. In the past, he also served as Deputy Dean of the Faculty of Electrical Engineering and Deputy Rector for Organisation and Development at the West Pomeranian University of Technology. He is the current Head of the Department of Power Systems and Electrical Drives of the Faculty of Electrical Engineering. He is also a member of the Committee on Electrical Engineering of the Polish Academy of Sciences, the Polish Society of Theoretical and Applied Electrical Engineering, the Association of Polish Electrical Engineers, the International Magley Board, the International Compumag Society, Societas Humboldtiana Polonorum (as Vice-President in 2016-2019), the Polish Society of Applied Electromagnetism, and the Council of Scientific Excellence at the Ministry of Science and Higher Education (since 2019). He also serves as the chairman of the board at the Museum of Technology and Transport in Szczecin.
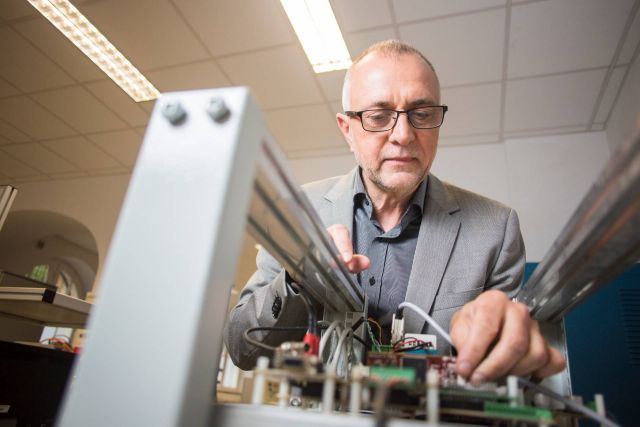